30.08.23
Ensuring your workers can safely use on-site tools and equipment
Construction safety
In the construction industry, the foundation of any successful project is an unwavering commitment to safety. From towering skyscrapers to intricate renovations, the use of on-site tools and equipment is crucial for construction work.
At City Hire, we recognize the significance of safeguarding workers and ensuring their adeptness in safely operating a wide range of tools and machinery. This extensive guide will delve into various aspects of construction safety, encompassing different categories of tools and equipment that are common in the industry.
Access Equipment
Access equipment, including scaffolding, ladders, and mobile elevated work platforms (MEWPs), provide elevation solutions for workers when working on complex structures.
Safety in using these tools requires adherence to certain standards:
- Regular inspection and maintenance of access equipment are pivotal to detect wear and tear that could lead to accidents.
- Comprehensive training for workers is essential, focusing on the proper use, setup, and dismantling of these tools.
- Fall protection measures, such as the utilisation of harnesses, guardrails, and safety nets, must be diligently practised to prevent falls from elevated positions.
- Strict observance of manufacturer guidelines regarding weight limits, load distribution, and usage protocols is crucial to avert equipment failure.
View our access equipment for hire.
Accommodation / Storage Welfare
While the physical act of construction tends to takes centre stage, providing suitable accommodation and welfare facilities for workers is just as important when it comes to ethical and practical construction management:
- Establishing clean, well-ventilated rest areas contributes to worker well-being and enhances their efficiency.
- The provision of easily accessible and hygienic toilet facilities is mandatory for maintaining worker health and morale.
- Adequate drinking water points and secure storage for personal belongings enable workers to perform optimally without discomfort.
View our accommodation, storage and welfare for hire.
Breakers & Drills
Breakers and drills are vital to construction and their operation demands caution and adherence to safety protocols:
- Adequate personal protective equipment (PPE), including safety goggles and ear protection, is vital in order to shield workers from flying debris and excessive noise.
- Routine inspection and maintenance of equipment components, such as drill bits and chisels, are paramount to ensure optimal functionality and prevent accidents.
- Secure the immediate work area and cordon it off from others to prevent unintended injuries caused by debris and tool movement.
View our breakers & drills for hire.
Cleaning
Construction sites are synonymous with dirt and debris which therefore makes cleanliness very important to ensure that everything is in order with construction health and safety:
- Prompt cleanup of spills and removal of debris which mitigate slip and fall hazards that could lead to injuries.
- Effective waste disposal practices prevent clutter and the potential risk of workers tripping over discarded materials.
View our cleaning equipment for hire.
Climate Control
Extreme weather conditions can adversely impact workers' health and safety on construction sites:
- Provision of climate control equipment, such as portable heaters and cooling fans can easily improve worker comfort, prevent weather-related health issues and improve site safety as a whole.
- Encouraging workers to take regular breaks in shaded or temperature-controlled areas during extreme weather conditions mitigates the risk of heat-related illnesses or cold stress.
View our climate control equipment for hire.
Concreting & Compaction
Concrete work necessitates precision and the adherence to construction health and safety guidelines:
- Workers should wear appropriate PPE, including gloves, eye protection, and respiratory masks to guard against contact with concrete dust and potential chemical irritants.
- Thorough training in concrete mixing, pouring, and finishing techniques is vital to avert splashes, spills, and inadvertent contact with wet concrete.
- Workers using vibrating equipment should be educated about the risks of hand-arm vibration syndrome and the necessity of taking adequate breaks to prevent long-term health issues.
View our concreting for hire.
Cutting & Grinding
Using tools like angle grinders and saws on site demand a deep awareness of construction safety measures:
- Workers must be equipped with respiratory protection to shield against inhalation of hazardous dust and particulates generated during cutting and grinding operations.
- Safety guards integrated into tools should never be tampered with, as they are designed to prevent accidental contact with the cutting or grinding mechanisms.
- Designated cutting areas should be established to minimise risks to other workers who might be nearby during these operations.
View our cutting & grinding equipment for hire.
Fencing & Barriers
Fencing and barriers serve as boundaries to ensure site security, as well as safety for construction workers, preventing them from being exposed to any potential health and safety hazards:
- Routine inspection of fencing for structural integrity and damage is necessary, with prompt repairs or replacements being carried out when required.
- Clear and prominently visible warning signs must be positioned in the vicinity of hazardous areas, indicating the presence of potential dangers.
View our fencing & barriers for hire.
For more information on construction site security with fencing and barriers, check out our recent article. Fences & Barriers: A comprehensive guide to keeping your construction site secure.
Fixing & Fastening
Nails, screws, and fasteners are present all over a construction site. To maximise your site safety, you should consider:
- The issuance of suitable eye protection to workers is imperative to shield against potential eye injuries caused by flying debris during fixing and fastening activities.
- Ergonomic practices, encompassing proper posture and lifting techniques, should be emphasised to prevent strains and repetitive stress injuries associated with these tasks.
View our fixing and fastening equipment for hire.
Fuel & Gas
The handling of flammable materials demands an acute awareness of site safety precautions:
- Storage of fuel and gas containers in well-ventilated, fire-resistant cabinets away from potential ignition sources prevents the escalation of minor accidents into major conflagrations.
- Education of workers regarding proper handling, storage, and emergency procedures in the event of a gas leak or spillage is indispensable to minimise risks.
View our fuel and gas equipment for hire.
Landscaping & Gardening
Landscaping and gardening necessitate adherence to safety standards:
- Provision of appropriate outdoor PPE, including sun hats, sunscreen, and insect repellent, safeguards workers from the perils of outdoor work.
- Training workers to identify poisonous plants and potentially hazardous insects prevents inadvertent contact and resultant health complications.
View our landscaping and gardening equipment for hire.
Lifting Equipment
The operation of cranes, hoists, and other lifting equipment demands both expertise and compliance with safety norms to comply with health and safety on construction sites:
- Only certified operators should be entrusted with the operation of lifting equipment, after undergoing specialised training and evaluation.
- Rigorous and periodic inspection of equipment components, load-bearing mechanisms, and rigging is critical to avert potential accidents.
- During lifting operations, the establishment of a safe distance between workers and the load being lifted is fundamental to prevent the occurrence of accidents caused by falling materials.
View our lifting equipment for hire.
Lighting
Adequate lighting is important in order to to prevent accidents on site, particularly in poorly lit environments:
- Illuminated pathways and well-lit work areas mitigate the likelihood of trips, falls, and collisions caused by inadequate visibility.
- Temporary lighting solutions should be employed in areas without permanent lighting fixtures to ensure consistent visibility and site safety.
View our lighting equipment for hire.
Material Handling
Proper material handling practices are indispensable to prevent physical strain and accidents:
- Workers should receive comprehensive training in ergonomics and proper lifting techniques to safeguard against musculoskeletal disorders.
- Mechanical aids, including wheelbarrows, trolleys, and conveyors, should be furnished to facilitate the movement of heavy or bulky materials, reducing the risk of worker injuries.
View our materials handling equipment for hire.
Mechanical & Electrical
There is a wide range of mechanical and electrical tools and equipment that will need meticulous training and adherence to safety protocols in order to comply with construction health and safety:
- Workers operating complex machinery must undergo extensive training, ensuring familiarity with machine controls, emergency shutdown procedures, and proper maintenance practices.
- Regular equipment checks and maintenance are paramount to detect potential malfunctions or wear and tear, preventing unexpected breakdowns that could endanger workers.
View our mechanical and electrical equipment for hire.
Plant
Plant machinery, such as excavators, bulldozers, and loaders, require a distinct level of expertise and safety awareness:
- Only operators possessing appropriate certifications and qualifications should operate plant machinery, after undergoing comprehensive training in machine operation, maintenance, and safety protocols.
- NVQs (National Vocational Qualifications) in Construction Plant Operations: When operating specific mechanical and engineering equipment on UK construction sites, possessing the relevant CPCS card is frequently obligatory. These cards serve as evidence that the operator has been evaluated for their ability to use the equipment safely.
- PCS (Construction Plant Competence Scheme) Cards: When operating specific mechanical and engineering equipment on UK construction sites, possessing the relevant CPCS card is frequently obligatory. These cards serve as evidence that the operator has been evaluated for their ability to use the equipment safely.
- The delineation of clear exclusion zones and the consistent enforcement of safety barriers around operating plant machinery prevent accidents arising from worker proximity to active machinery.
View our plant machinery for hire.
Powered Access
Operating powered access equipment, such as a scissor lift, typically requires proper training and qualifications to ensure the safety of both the operator and those around them.
- Training Program: Most countries have training programs specifically designed to teach individuals how to safely operate powered access equipment. These training programs cover topics such as equipment controls, safety procedures, hazard recognition, emergency protocols, and more.
- CPCS (Construction Plant Competence Scheme) Cards:
- IPAF PAL Card: The International Powered Access Federation (IPAF) offers a widely recognized training program for operating powered access equipment. Completing this training and passing the associated exam can result in receiving an IPAF PAL (Powered Access Licence) Card. This card serves as proof of the operator's training and competence in operating different types of powered access equipment.
- Operator's Manual: Familiarity with the operator's manual of the specific scissor lift model you will be operating is crucial. The manual provides essential information about the machine's controls, safety features, maintenance requirements, and operational guidelines.
- Site-Specific Training: In addition to general training, operators should receive site-specific training that covers any unique hazards, regulations, or conditions present at the specific worksite where the equipment will be used.
- Safety Regulations and Standards: Operators should be familiar with relevant safety regulations and standards set by government authorities and industry organisations. These regulations may cover aspects such as equipment maintenance, inspection routines, and safety precautions.
- Valid Licence: Depending on the jurisdiction, operators might need a valid driver's licence or another type of permit to operate powered access equipment legally.
- Physical Fitness: Operating powered access equipment can involve physical demands, such as climbing onto the platform or using controls. Operators should be in good physical condition to perform these tasks safely.
View our powered access for hire.
It's important to note that these qualifications and requirements can vary depending on where you are located and the specific industry you're working in.
Always ensure that you are complying with the regulations and standards set by your local authorities and industry organisations.
Power & Electrics
Electrical tools pose inherent shock and fire hazards:
- The diligent examination of cords, plugs, and insulation for signs of wear, fraying, or damage is essential to prevent electrocution and equipment malfunction.
- The installation of Ground Fault Circuit Interrupters (GFCIs) within circuits diminishes the risk of electric shocks by rapidly disconnecting power in the presence of a ground fault.
View our power and electrics for hire.
Propping & Support
Temporary propping and support systems are integral to ensuring structural stability and building site health and safety:
- Propping and support systems should be meticulously designed by qualified engineers, accounting for load-bearing capacities and stress distribution to prevent structural failures.
- Workers should be aware of designated safe working loads for propping equipment.
- Adhering to these limits can prevent accidental overloading and subsequent collapse.
View our propping and support equipment for hire.
Sanding & Woodworking
Dust generated during sanding and woodworking activities poses respiratory and fire hazards:
- To maximise site safety, construction workers must be equipped with respiratory protection, comprising properly fitting masks, to mitigate the inhalation of hazardous airborne particles.
- Dust extraction systems and local exhaust ventilation should be used to effectively capture and remove airborne dust, ensuring a safe and clean working environment as well as adhering to construction health and safety measures.
View our sanding and woodworking tools for hire.
Site Equipment & Groundworks
An assortment of equipment is used in ground preparation. For construction site safety, workers should comply with safety norms:
- Workers engaging in tasks like earthmoving, trenching, or foundation laying should be outfitted with suitable PPE, including gloves and sturdy footwear, to prevent abrasions and lacerations.
- The implementation of clear communication protocols among workers prevents accidents arising from misunderstandings or miscommunications during groundworks.
View our site equipment and groundworks for hire.
Conclusion
The assurance of worker safety during the utilisation of on-site tools and equipment is something that requires unwavering commitment, comprehensive training, and adherence to established industry practices.
By prioritising construction site safety considerations across diverse categories like access equipment, cutting tools and landscaping, construction companies can substantially mitigate the risks of accidents, injuries, and potentially catastrophic incidents.
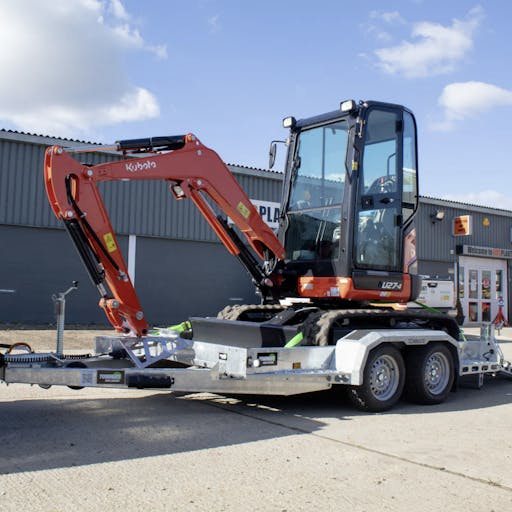