26.05.23
Hiring vs Buying: What's Best for Me and My Projects?
Deciding whether to hire or buy your tools and equipment is so important. Your choice can affect the productivity, prices and overall efficiency of your project, plus so much more. There are plenty of advantages and disadvantages for both.
You should consider your needs and the needs of the project you are working on before making a decision.
Think about:
- Savings
- Project costs
- Tax implications
- Capital expenditure
- Equipment upgrades
- Congestion charges and O licences
- The advantages of using new equipment
- Storage, transportation and maintenance
Advantages of hiring
Better Cost Control
Flexibility is one of the main advantages of hiring. Different tools and equipment are constantly needed for construction projects and companies that choose to hire can easily gain access to a variety of equipment in an instant.
Better project planning and adaptability is possible when hiring and ensures that the appropriate tools are available when needed on site.
With hire you can accurately control the overall cost of your projects. When you buy your own equipment, it is hard to account for as the depreciation hits your overheads, regardless of what projects you are working on.
Capital Expenditure
Cash is king. Tying up your cash in machinery isn’t wise and can lead to problems down the line. Buying machinery outright will hit your budget hard and it isn’t commercially viable to pay finance on machines that aren’t used very often. Once you also consider the expensive interest rates when financing items, it becomes clear that hiring is the way to go, especially with expensive tools and equipment.
Huge upfront investments are avoided when hiring tools and equipment. Hiring allows businesses to use their capital for other important areas of their business, such as marketing or recruitment which tend to require some financial backing.
Storage & transportation
Buying construction tools and equipment comes with a number of challenges that can be avoided when hiring, including the need for storage, transportation and security arrangements.
Here are some examples of the cost range for storage:
- Self-storage units
- Warehouse storage
- Basic self-storage units: £8 - £20 per square foot
- High-end or premium units with enhanced security features: £25 - £40+ per square foot
- Industrial warehouses: £4 - £12 per square foot
- Fulfilment or distribution centres: £8 - £18 per square foot
The average cost per square foot for storage space (which varies depending on location, type of facility and other factors) is thought to be around £20 - £25 weekly.
By hiring, you will completely eradicate these costs – your hire company will take care of all your transportation and storage needs.
Without any need for transportation, you re also preventing additional costs. For example, you wouldn’t need to pay salaries for any drivers that you would have to employ to transport your equipment. You would also avoid having to pay for and run a van or lorry every day.
Factors such as fuel, insurance and road tax can all be avoided by letting your hire company deal with the transportation of your tools and equipment.
At City Hire, you can arrange for same or next day delivery, as well as pick up within two working days - keeping our service fast and frictionless.
Maintenance
Hire companies take care of all maintenance and repairs. This saves time and resources as the responsibility of maintaining and servicing the machinery is purely down to us.
The risk of breakdowns during your project is also decreased, as City Hire will ensure that the tools and equipment provided are well-maintained and have passed any required compliance checks, allowing you to get started with the task at hand as soon as possible.
Tax Benefits
Hiring costs can be deducted as a business expense. This, in turn, will give construction companies some tax advantages that they wouldn't have had if they purchased their tools and equipment. Businesses that hire tools and equipment can offset hire costs against their taxable income, which also lowers their overall tax liability.
We would recommend that you speak with tax experts and accountants to find out about the possible tax advantages for your line of work.
Disadvantages of hiring
Higher costs long-term
Whilst hiring may seem like the more affordable option out of the two, hiring for an extended period will eventually mount up. To figure out if buying is a better option than hiring equipment, construction companies should consider the duration and frequency of their tool and equipment usage. In addition, hire rates could change based on the demand of a certain item, which could also increase costs.
Limited Equipment Availability
Some equipment might not be available with particular hire companies depending on location and current demand. This could be detrimental for an on-going construction project that requires specialised equipment or tools which may not be available in hire fleets.
Companies will need to look at alternative choices or perhaps even think about buying the machinery to guarantee that they can continue with their project and stick to any deadlines.
Advantages of buying
Long-term cost Savings
Buying tools and equipment could turn out to be more cost effective for the long term, particularly for items that will be used often. You will avoid any ongoing hire expenses when you purchase your equipment. These expenses can add up over time and end up costing more than the initial expenditure.
In short, construction companies can save money by buying the equipment, especially if they frequently or continuously need a certain item that isn't too expensive to purchase outright.
Upgrades
When your company owns a piece of equipment, you can update or modify it to suit the demands of a particular project. Owning the tools gives you the freedom to upgrade or invest in more advanced machines, increasing productivity, efficiency, and the standard of work on site.
Construction technology and equipment capabilities are constantly improving. The ability to modify and adapt equipment to meet the needs of particular projects can give you an advantage over other construction companies.
Availability
Buying and owning equipment means that it is always available when needed. Depending on some hire companies and their equipment could cause delays if any issues arise, such as availability.
Companies can better manage project timeframes. Owning the right tools and equipment reduces the room for any waiting around – you will just have to make sure that equipment is purchased and properly checked before you start your project!
Potential resale value
Depending on its condition and market demand, equipment can be sold when no longer required. This can help you to recover some of the initial investment and, in turn, lower the total cost of ownership.
Resale value varies based on elements like:
- Age of equipment
- Market demand
- Condition.
These are important to consider, as it can result in future financial advantages for you and your company.
Disadvantages of buying
Capital Expenditure
A large down payment is necessary when buying tools and equipment. To ensure that you can afford to buy the required tools and equipment, you will have to look over your financial resources and overall budget.
This capital expenditure will take up a big portion of a company's budget, which is money that could be used to fund other aspects of the company and its projects.
Storage and maintenance
Buying equipment means that you will have to set up and maintain storage facilities. You will also need to consider protection from theft and damages. Construction tools and equipment will need to be stored in a safe and secure place. Storage for equipment will also add to your overall costs, especially if you have a large collection of equipment.
Companies will also need to maintain and service the equipment with any maintenance and repairs. Having to source any required parts would take up a significant amount of time and could hinder any deadline-driven projects.
Maintenance takes up time and resources, as well as needing previous experience if it was to be done internally. Your company would require special training and would have to pass thorough examinations in order to have specialist certifications, such as a LOLER certification.
Externally, it would be very expensive to get your equipment tested by an external maintenance company which usually have very high mark-ups on repairs and services.
Transportation
Companies that own their own vehicles and equipment will run into extra costs, especially in London. This is due to the costs that come with running a vehicle and ensuring that you can legally keep it on the road, such as O licensing and congestion charges.
The potential expenses of running a van or lorry for your transportation needs include:
- Cleaning
- Insurance
- Road Tax
- Fuel costs
- Parking fees
- Congestion charges
- Vehicle depreciation
- Maintenance and repairs
- Vehicle purchase or lease
You will need to take into account the extra costs that are involved when working in busy, populated areas and must acquire the required licences to abide by the law and continue to operate.
Recap
Hiring or buying construction tools and equipment requires a lot of thought and consideration. You should only decide between one or the other after carefully going over all of the above considerations.
Hiring offers:
- Flexibility
- Potential tax benefits
- Cost effective for short term projects
- Avoids significant capital expenditure
- Access to a wide range of equipment
- Maintenance and servicing done for you
- Peace of mind and eliminates storage and transportation concerns
However, it can end up being more expensive over time, depending on the tool or equipment.
Buying equipment comes with:
- Large upfront expenses,
- Storage and maintenance duties
- Potential regulatory issues like London congestion fees and O licencing.
However, buying tools and equipment also offer:
- 24/7 equipment availability
- Potential asset value and resale value
- Full ownership and control of equipment
- Long-term cost benefits and better project cost control for frequent, long-term equipment needs.
Before making a decision, you should carefully look over:
- Budget
- Project requirements
- Long-term business objectives
When deciding whether to hire or buy construction tools and equipment, you should take into account:
- Project scale
- Financial limits
- Direction of the company
- The needs of the company
A project that combines hiring and buying seems like the best option. This way, construction companies can balance flexibility and cost-effectiveness whilst also ensuring that the best possible tools and equipment are available when needed.
Construction companies should choose the option that maximises efficiency, whilst also reducing costs where possible to support their long-term success.
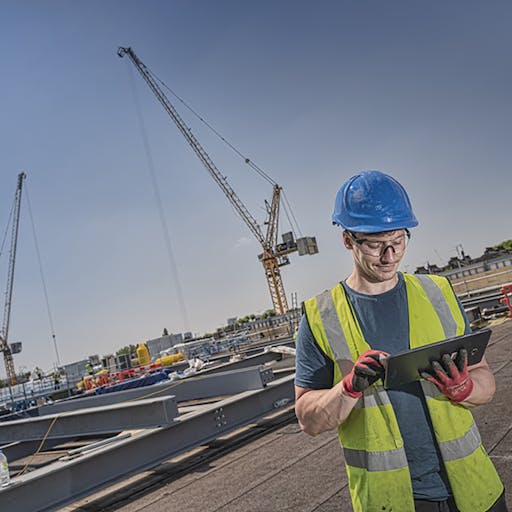