24.05.23
Everything you need to know about Chain Blocks
What are Chain Blocks?
Chain blocks, also known as chain hoists or chain pulleys, are mechanical devices used for lifting and moving heavy loads in various industries and applications. They are a type of manual lifting equipment that utilizes a system of chains and gears to provide mechanical advantage and facilitate lifting operations.
The main components of a chain block include a load chain, a hand chain, a lifting hook, and a chain block body. The load chain is made up of interlinked metal chains that form a loop, capable of supporting the weight of the load. The hand chain is used to operate the chain block by pulling or releasing it, which causes the load chain to move through the block body.
The chain block body contains gears and sprockets that engage with the load chain. When the hand chain is pulled, it rotates the gears, causing the load chain to move, and subsequently lifting the load. The lifting hook is attached to the load chain and is used to secure the load during lifting.
Chain blocks are available in various capacities, ranging from a few hundred kilograms to several tons, allowing them to handle a wide range of lifting tasks. They are often used in construction sites, manufacturing facilities, warehouses, and other industrial settings where lifting and moving heavy objects are required.
It's important to note that while chain blocks provide mechanical advantage and make lifting easier, they still require proper handling, safety precautions, and adherence to weight capacity limits to prevent accidents and ensure safe lifting operations.
What types of Chain Block are there?
There are several types of chain blocks available, each designed for specific lifting applications. Here are some common types:
Manual Chain Block: This is the most basic type of chain block and is operated manually using a hand chain. It is suitable for general lifting tasks and is often used in construction sites, workshops, and small-scale industrial applications.
Lever Chain Block: Also known as a lever hoist, this type of chain block utilizes a lever mechanism instead of a hand chain. It allows for easier operation by utilizing a ratcheting system, where the lever is pulled back and forth to lift the load. Lever chain blocks are compact and suitable for confined spaces.
Electric Chain Block: Electric chain blocks are powered by an electric motor and are controlled using a pendant or remote control. They offer convenient and efficient lifting operations, especially for heavy loads or frequent lifting tasks. Electric chain blocks are commonly used in industrial environments where manual lifting is impractical or labor-intensive.
How do you use a chain block?
Using a chain block requires careful adherence to safety guidelines and proper operating procedures. Here is a general step-by-step guide on how to use a chain block:
Assess the Load: Before using a chain block, evaluate the weight and dimensions of the load to ensure it is within the capacity of the chain block. Exceeding the weight limit can lead to equipment failure or accidents.
Inspect the Chain Block: Thoroughly inspect the chain block before use. Check for any signs of damage or wear, such as cracks, bent components, or frayed chains. Ensure that all parts, including hooks and attachments, are in good working condition.
Choose the Proper Anchoring Point: Identify a secure and suitable anchoring point from which to suspend the chain block. The anchor should be capable of supporting the weight of the load and provide adequate clearance for lifting.
Attach the Chain Block: Attach the upper hook of the chain block to the anchoring point securely. Ensure that the hook is properly engaged and positioned to prevent it from slipping or coming loose during lifting.
Position the Load Hook: Lower the load hook of the chain block to the level of the load. Ensure that the hook is properly positioned and securely attached to the load. Make sure the load is balanced and properly rigged to avoid any tipping or instability.
Apply Tension to the Hand Chain: Begin pulling the hand chain in a steady and controlled manner. The load chain will start to move through the chain block, gradually lifting the load. Continue pulling the hand chain until the load reaches the desired height.
Monitor the Lifting Process: Keep a close eye on the lifting process to ensure smooth and controlled movement. Avoid sudden jerks or rapid pulling of the hand chain. Use the hand chain to stop or lower the load when necessary.
Secure the Load: Once the load has reached the desired position, secure it using appropriate means such as shackles, slings, or other approved fastening methods. Ensure that the load is properly secured to prevent accidental release or movement.
Release the Tension: To lower the load, slowly and carefully release tension from the hand chain. Avoid rapid or uncontrolled lowering, as it can cause damage or accidents.
Store the Chain Block: After use, store the chain block in a suitable location, protected from environmental hazards, and in a way that prevents damage or entanglement of the chains and hooks.
What certification do Chain Blocks need?
Chain blocks, like other lifting equipment, often require certification to ensure their safety and compliance with relevant standards.
In many jurisdictions, including the United Kingdom, chain blocks are subject to the Lifting Operations and Lifting Equipment Regulations (LOLER). LOLER is a set of regulations that apply to the use of lifting equipment, including chain blocks, in the workplace. These regulations aim to ensure the safe use of lifting equipment and protect workers from the risks associated with lifting operations.
Under LOLER, employers and duty holders are required to meet certain obligations, which include:
Thorough Examination: Chain blocks and other lifting equipment must undergo periodic thorough examination by a competent person. This examination is conducted to assess the equipment's safety, integrity, and proper functioning. The frequency of the examination depends on various factors, such as the type of equipment, its intensity of use, and the environment in which it is used.
Certification and Record-Keeping: A thorough examination of a chain block should result in the issuance of a certificate of thorough examination. This certificate confirms that the chain block has been examined, found to be safe and in proper working condition. It should include details of the equipment, examination dates, and the name of the competent person. The employer or duty holder is responsible for maintaining records of thorough examinations and making them available for inspection.
Safe Use and Inspection: Employers and duty holders must ensure that chain blocks are used safely and inspected regularly. This includes providing proper training and instruction to operators, establishing safe working procedures, and conducting routine inspections to identify any defects or issues that may affect the equipment's safety.
Risk Assessment: Employers and duty holders are required to conduct risk assessments for lifting operations involving chain blocks. The risk assessment helps identify potential hazards, assess the risks associated with the lifting task, and implement appropriate control measures to mitigate those risks.
It is important to note that the specific requirements and regulations may differ depending on the jurisdiction. Employers and duty holders should consult the relevant local regulations, such as LOLER in the UK, to ensure compliance with the specific certification and inspection requirements for chain blocks.
What type of chains do Chain Blocks have?
In the context of chain blocks, "G8" and "G10" refer to the grade of the load chain used in the equipment. Here's what each grade represents:
G8 (Grade 80)
G8 load chains are made from high-strength alloy steel and are designed to withstand heavy loads and demanding lifting tasks. Grade 80 chains have a higher working load limit (WLL) compared to lower-grade chains. They undergo a heat treatment process to enhance their strength, durability, and resistance to wear and fatigue. G8 chains are known for their high safety factor, typically having a breaking strength four times higher than the maximum working load.
G10 (Grade 100)
G10 load chains are an even higher grade of load chain than G8. They offer increased strength, durability, and load-bearing capacity. Grade 100 chains are commonly used in heavy-duty lifting applications where exceptional strength and reliability are required. They provide a higher working load limit and breaking strength compared to G8 chains.
Both G8 and G10 load chains are designed to be used with chain blocks and other lifting equipment rated for their respective grades. The choice between G8 and G10 chains depends on the specific lifting requirements, load capacity, and safety factors associated with the lifting operation.
What do you attach Chain Blocks to?
Chain blocks are typically attached to a suitable anchoring point or lifting structure to safely suspend and lift loads. The specific attachment method will depend on the application and available infrastructure. Here are some common options for attaching chain blocks:
Overhead Beams or Girders: Chain blocks are often attached to overhead beams or girders that are specifically designed to support lifting operations. These beams are typically made of steel and are capable of withstanding the weight of the load being lifted. Chain blocks can be connected to the beams using suitable clamps, trolleys, or beam attachments.
Jib Cranes: Jib cranes are freestanding or wall-mounted structures with a horizontal jib arm. Chain blocks can be attached to the jib arm using appropriate mounting brackets or trolleys. Jib cranes provide a versatile lifting solution and can be positioned to cover specific areas or workstations.
Gantry Cranes: Gantry cranes are overhead cranes supported by a framework of vertical legs and horizontal beams. Chain blocks can be attached to the horizontal beams of the gantry crane using clamps, trolleys, or other compatible attachments. Gantry cranes are often used in outdoor environments or when a fixed overhead structure is not available.
Lifting Frames or Spreaders: In some cases, chain blocks may need to be attached to lifting frames or spreader bars to distribute the load more evenly. Lifting frames or spreaders are structures with multiple attachment points that allow for balanced lifting of bulky or irregularly shaped loads. The chain blocks can be connected to the lifting frame or spreader using appropriate hooks or attachments.
Rigging Points: Depending on the specific lifting task and available infrastructure, chain blocks can also be attached to designated rigging points, such as eye bolts, hooks, or other load-bearing fixtures that are securely fastened to a structure. It is crucial to ensure that the rigging points are rated and capable of supporting the intended load.
When attaching chain blocks, it is essential to follow the manufacturer's recommendations and guidelines for proper installation. Additionally, consulting with a qualified engineer or lifting specialist can provide valuable insights into selecting the appropriate attachment points and ensuring the overall safety of the lifting operation.
What are the advantages and disadvantages of using Chain Blocks?
Using chain blocks offers several advantages, but there are also some disadvantages to consider. Here are some of the key advantages and disadvantages of using chain blocks:
Advantages:
Versatility: Chain blocks are available in a wide range of capacities, making them suitable for lifting various loads, from light to heavy. They can be used in diverse industries and applications, including construction, manufacturing, maintenance, and more.
Portability: Chain blocks are relatively lightweight and portable compared to other lifting equipment, such as cranes or hydraulic systems. This makes them easier to transport and maneuver, especially in confined spaces or temporary worksites.
Cost-Effectiveness: Chain blocks are generally more affordable than more complex lifting systems. They offer a cost-effective solution for lifting tasks that don't require continuous or high-capacity lifting operations.
Simple Operation: Chain blocks are manually operated using a hand chain, which makes them easy to use and control. The basic mechanics involve pulling or releasing the hand chain to lift or lower the load, requiring minimal training or technical expertise.
Mechanical Advantage: Chain blocks utilize a system of gears and pulleys, providing mechanical advantage that allows users to lift heavier loads with less effort compared to manual lifting alone.
Disadvantages:
Limited Lifting Height: Chain blocks have a limited lifting height, as they rely on the length of the load chain and the available space for manual operation. For lifting tasks that require significant height, alternative lifting systems such as cranes may be more suitable.
Manual Labour Intensive: While chain blocks provide mechanical advantage, they still require manual pulling or releasing of the hand chain. This can be physically demanding, especially for prolonged or repetitive lifting operations.
Limited Speed Control: Chain blocks offer limited control over the lifting speed. The lifting or lowering process is directly linked to the speed at which the hand chain is operated, which may not allow for precise or controlled movements in certain scenarios.
Noise and Maintenance: Chain blocks can generate noise during operation, particularly due to the metal-on-metal contact of the chains and gears. Regular maintenance is necessary to keep the chain block in good working condition, including lubrication, inspection of chains and hooks, and replacement of worn-out parts.
What are some alternative equipment to Chain Blocks?
There are several alternative equipment options available for lifting tasks, depending on the specific requirements and conditions. Here are some commonly used alternatives to chain blocks:
Electric Hoists: Electric hoists are powered lifting devices that use an electric motor for lifting and lowering loads. They offer controlled and efficient lifting operations, with features such as variable speed control and remote operation. Electric hoists are suitable for heavier loads or tasks that require frequent and precise lifting.
Wire Rope Hoists: Wire rope hoists utilize a wire rope instead of a chain for lifting operations. They offer higher lifting capacities and longer lifting heights compared to chain blocks. Wire rope hoists are commonly used in industrial settings, construction sites, and large-scale lifting applications.
Hydraulic Lifts: Hydraulic lifts use hydraulic power to raise and lower loads. They are often used in automotive garages, industrial environments, and warehouses. Hydraulic lifts can handle heavy loads and offer smooth and controlled lifting motions.
Lever Hoists: Lever hoists, also known as ratchet lever hoists or come-alongs, are manual lifting devices similar to chain blocks. They use a lever mechanism to lift and lower loads. Lever hoists are portable, compact, and suitable for lighter loads or applications where space is limited.
Pneumatic Hoists: Pneumatic hoists, also called air hoists, operate using compressed air to lift and lower loads. They are often used in environments where electric or hydraulic power is not ideal or feasible, such as in explosive or hazardous areas. Pneumatic hoists offer high lifting capacities and can be suitable for heavy-duty lifting operations.
Cranes: Cranes are large, specialized lifting machines used for heavy-duty lifting tasks. They come in various types, including tower cranes, mobile cranes, overhead cranes, and gantry cranes. Cranes offer significant lifting capacities, extended reach, and precise positioning capabilities. They are commonly used in construction sites, shipping ports, and industrial facilities.
The choice of alternative equipment will depend on factors such as the weight and type of loads, lifting height, available power sources, and specific requirements of the lifting task. It is important to assess the needs and consult with experts or suppliers to determine the most suitable alternative equipment for a particular application.
What lifting accessories are commonly used with Chain Blocks?
Several lifting accessories are commonly used in conjunction with chain blocks to enhance their functionality and ensure safe and efficient lifting operations. Here are some of the commonly used lifting accessories with chain blocks:
Slings: Slings are flexible straps or chains used to connect the load to the chain block. They provide a secure attachment point and distribute the load's weight across a wider area. Slings come in various types, including web slings, wire rope slings, and chain slings, and their selection depends on factors such as load weight, shape, and material handling requirements.
Shackles: Shackles are used to connect the slings or lifting hooks to the load or other lifting accessories. They provide a strong and secure connection point and come in various types, such as bow shackles and dee shackles. Shackles should be properly rated for the intended load capacity and ensure proper alignment and engagement to prevent accidental release.
Lifting Beams or Spreaders: Lifting beams or spreaders are structural components used to distribute the load and maintain balance during lifting. They provide multiple attachment points for slings or chain blocks, allowing for more controlled lifting of long, wide, or irregularly shaped loads. Lifting beams or spreaders help prevent load shifting or tilting during lifting.
Hooks: Hooks are integral components of chain blocks and are used to connect to the load or other lifting accessories. They come in various configurations, such as clevis hooks and grab hooks, and should have proper load ratings to match the chain block's capacity. Hooks should be securely engaged with the load or attachment points to prevent accidental detachment.
Rigging Hardware: Various rigging hardware, such as turnbuckles, eye bolts, and swivels, may be used depending on the lifting application. Rigging hardware facilitates the connection between the load, slings, and chain blocks, allowing for adjustments, rotations, or alignment as needed.
Spreader Bars: Spreader bars, also known as lifting beams, are specialized lifting accessories used to maintain load stability and control during lifting. They consist of a rigid bar with attachment points at each end for connecting the slings or chain blocks. Spreader bars help prevent load damage, ensure even weight distribution, and reduce the risk of load tipping or swinging.
Lifting Magnets or Vacuum Lifters: In specific applications where the load is ferromagnetic or has a smooth and non-porous surface, lifting magnets or vacuum lifters may be used with chain blocks. Lifting magnets use magnetic force, while vacuum lifters use suction to grip and lift loads without the need for slings or hooks.
It's important to ensure that all lifting accessories are properly rated, inspected, and used in accordance with manufacturer guidelines and applicable safety standards. The selection of lifting accessories depends on the specific lifting task, load characteristics, and safety requirements. Consulting with lifting specialists or professionals can help ensure the proper selection and use of lifting accessories with chain blocks.
How do you know if a chain block is safe to use?
To determine if a chain block is safe to use, it is essential to assess its condition, functionality, and compliance with safety standards. Here are some key steps and factors to consider when evaluating the safety of a chain block:
Valid LOLER Ticket: It's vital to ensure that the chain block has an in-date LOLER certificate signed by a competent person. LOLER certificates expire after 6 months. The chain is tested with the chain hoist so double check that the chain length matches what's recorded on the LOLER certificate.
Visual Inspection: Conduct a thorough visual inspection of the chain block. Look for signs of wear, damage, or deformation in the chain links, hooks, gears, and other components. Check for any visible cracks, corrosion, or bent parts. Ensure that all labels, markings, and safety information are present and legible.
Load Capacity and Rating: Verify that the chain block is suitable for the intended lifting task in terms of its load capacity. The load capacity should be clearly marked on the chain block. Ensure that the load to be lifted falls within the specified capacity. Do not exceed the rated capacity, as it can compromise the safety and integrity of the chain block.
Chain and Hooks: Inspect the load chain for wear, elongation, or damage. Check the chain for any twisted or kinked links. Inspect the hooks for signs of deformation, cracks, or latch malfunction. Ensure that the hooks close and lock properly and that the safety latch functions effectively. Replace any damaged or worn-out chain or hooks.
Lubrication: Check if the chain block is adequately lubricated. Proper lubrication helps ensure smooth operation and prevents excessive wear and friction. Apply appropriate lubricants as recommended by the manufacturer.
Operation and Functionality: Test the chain block's operation and functionality. Operate the chain block through its entire range of motion, lifting and lowering a light load if possible. Ensure that the hand chain moves freely and smoothly without any excessive resistance or binding. Check for any unusual noises or vibrations during operation.
Thorough Examination: Ensure that the chain block has undergone a recent thorough examination by a competent person. The thorough examination should be conducted at regular intervals as specified by regulations or standards applicable in your jurisdiction. Review the thorough examination certificate and ensure that it is up to date and valid.
How do you safely store Chain Blocks
To safely store chain blocks, consider the following guidelines:
Clean and Inspect: Before storing the chain blocks, clean them to remove any dirt, debris, or contaminants. Conduct a visual inspection to ensure there are no visible signs of damage or wear that could affect their safety and performance.
Suitable Storage Location: Choose a suitable storage location that is dry, well-ventilated, and protected from extreme temperatures, moisture, corrosive substances, and direct sunlight. Chain blocks should be stored indoors whenever possible to minimize exposure to environmental factors.
Proper Hanging: Hang the chain blocks vertically when storing them. This helps prevent any stress or strain on the load chain and ensures the chain block remains in good condition. Avoid hanging them directly on sharp edges or surfaces that could cause damage.
Secured Storage: Ensure that the stored chain blocks are secure and protected from unauthorized access or tampering. Consider using lockable cabinets, storage rooms, or dedicated areas to prevent accidental or unauthorized use.
Avoid Overloading: Do not stack or store heavy objects on top of the chain blocks, as this can cause damage or deformation. Keep them separate from other equipment or materials to avoid potential accidents or entanglement.
Lubrication: Apply a thin layer of suitable lubricant to the load chain and other moving parts of the chain block before storage. This helps prevent corrosion and ensures smooth operation when the chain blocks are next used.
Proper Storage Hooks or Racks: Use appropriate storage hooks or racks designed specifically for chain blocks. These hooks or racks should securely support the weight of the chain blocks without causing any stress or damage to the load chain or other components.
Documentation and Inspection: Maintain proper documentation of inspections, certifications, and maintenance records for the stored chain blocks. Keep the documents in a secure and easily accessible location for reference and inspection purposes.
Regular Maintenance: Even during storage, periodically check the stored chain blocks to ensure they remain in good condition. Inspect them for any signs of deterioration or damage that may have occurred during storage, and address any issues promptly.
By following these storage guidelines, you can help ensure that chain blocks remain in a safe and serviceable condition for their next use. Remember to refer to the manufacturer's recommendations and any applicable regulations or standards specific to your location for additional guidance on the safe storage of chain blocks.
How do you lubricate Chain Blocks and what lubricant do you use?
Lubricating chain blocks is an important maintenance task that helps ensure smooth operation and prolong the lifespan of the equipment. Here's a general guide on how to lubricate chain blocks and the recommended lubricant to use:
Clean the Chain Block: Before applying lubricant, clean the chain block to remove dirt, debris, or old lubricant that may have accumulated. Use a soft brush or cloth to wipe down the load chain, gears, and other moving parts.
Choose the Right Lubricant: Select a lubricant specifically designed for chain blocks and suitable for the operating conditions. It's recommended to use a high-quality, lightweight oil or chain lubricant that provides excellent lubrication, corrosion protection, and has good adhesive properties. Consult the manufacturer's recommendations or guidelines to identify the most suitable lubricant for your specific chain block model.
Apply Lubricant to the Load Chain: Apply a small amount of lubricant to the load chain by dripping or spraying it along the chain's length. Ensure that the lubricant reaches all the chain links, rollers, and pins. Move the load chain manually or operate the chain block to allow the lubricant to penetrate and distribute evenly.
Lubricate Other Moving Parts: Apply lubricant to other moving parts of the chain block, such as gears, bushings, bearings, and hooks. Use a brush or applicator to apply the lubricant precisely to these areas. Ensure that the lubricant reaches all the necessary contact points to reduce friction and promote smooth movement.
Remove Excess Lubricant: After applying the lubricant, wipe off any excess oil or lubricant using a clean cloth. Excessive lubrication can attract dust, dirt, or debris, leading to potential blockages or performance issues.
Periodic Lubrication: Regularly lubricate the chain block as part of routine maintenance. The frequency of lubrication depends on the manufacturer's recommendations and the frequency of use. In general, lubrication should be performed at regular intervals or whenever the chain block shows signs of stiffness, noise, or decreased performance.
Always refer to the manufacturer's guidelines for specific instructions on lubrication for your chain block model. Following the manufacturer's recommendations ensures that you use the correct lubricant and apply it in the appropriate manner, optimizing the performance and lifespan of the chain block.
Can Chain Blocks jam or break?
Yes, chain blocks can potentially jam or break under certain circumstances. While chain blocks are designed to be robust and reliable, various factors can contribute to jams or breakages. Here are some reasons why chain blocks can experience jams or failures:
Overloading: Exceeding the load capacity of the chain block is a common cause of failures. Putting excessive weight on the chain block can lead to overloading, causing the load chain to become jammed or the chain block's components to fail.
Incorrect Use: Improper use or operation of the chain block can result in jams or breakages. Pulling the hand chain at an incorrect angle, using jerky or sudden movements, or applying uneven forces can lead to the load chain becoming tangled or the gears getting stuck.
Misalignment or Improper Rigging: If the load is not properly aligned with the chain block or if the rigging accessories, such as slings or hooks, are not correctly attached, it can cause the load chain to twist or snag, resulting in a jam or breakage.
Wear and Tear: Over time, wear and tear can affect the components of the chain block. Worn or damaged load chain, hooks, gears, or bearings can increase the risk of jams or failures during operation.
Lack of Maintenance: Insufficient or inadequate maintenance can contribute to chain block failures. Without proper lubrication, cleaning, and periodic inspections, the chain block's components can wear out, leading to malfunctions or breakages.
Accidental Damage: Impact, dropping, or mishandling of the chain block can cause internal or external damage to its components, resulting in jams or breakages.
What capacities and lengths of Chain Block are there?
Chain blocks are available in various capacities and lengths to accommodate different lifting requirements. The specific capacities and lengths of chain blocks can vary between manufacturers and models. However, here are some common capacity and length ranges you may come across:
Capacity Range: Chain blocks are typically available in capacities ranging from as low as 0.25 tons (250 kg) to as high as 50 tons. However, in our experience a 1 ton, 2 ton, or 3 ton chain block is sufficient for most requirements.
Standard Length: The standard length of the load chain on a chain block is often around 3 meters (10 feet). This length is suitable for many lifting applications. However, longer load chain lengths are available for specific needs. Extended Length: For lifting applications that require a longer reach or greater lifting height, chain blocks with extended load chain lengths are available. These extended length chain blocks can have load chains ranging from 6 meters (20 feet) to 30 meters (100 feet) or more.
Customizable Lengths: Some manufacturers offer the flexibility to customize the length of the load chain according to specific requirements. This allows for tailoring the chain block to suit the lifting needs of a particular application.
When selecting a chain block, it is crucial to consider the weight of the loads to be lifted and the required lifting height. It's essential to choose a chain block with a suitable capacity and length that can safely handle the intended lifting tasks.
Keep in mind that the availability of specific capacity and length options may vary depending on the manufacturer and regional regulations. It's always recommended to consult the product specifications and consult with suppliers or experts to ensure the chain block meets your specific lifting requirements.
What are ATEX rated chain blocks?
ATEX rated chain blocks are specially designed and certified for use in potentially explosive atmospheres. ATEX is an abbreviation for "ATmosphères EXplosibles," which refers to the European Union directive for equipment and protective systems intended for use in explosive atmospheres.
ATEX rated chain blocks adhere to strict safety standards to minimize the risk of igniting flammable substances, gases, or dust particles in explosive environments. These chain blocks are commonly used in industries such as oil and gas, petrochemical, chemical, mining, and other hazardous environments where the presence of flammable materials or gases is a concern.
Here are some key features and requirements of ATEX rated chain blocks:
Construction: ATEX rated chain blocks are constructed using materials that minimize the risk of sparks or ignition. Non-sparking materials, such as aluminum-bronze or beryllium-copper alloys, are often used in critical components.
Surface Treatment: The surfaces of ATEX rated chain blocks undergo special treatment to minimize the risk of static electricity build-up, electrostatic discharge, or sparking.
Sealing: ATEX chain blocks feature enhanced sealing to prevent the entry of flammable gases, dust, or substances that could potentially cause an explosion.
Certification: ATEX rated chain blocks undergo rigorous testing and certification by authorized bodies to ensure compliance with the ATEX directive and relevant safety standards. The certification includes both mechanical and electrical aspects of the chain block.
Markings: ATEX rated chain blocks carry specific markings, such as the ATEX symbol, certification number, and relevant hazardous area classification codes, to indicate their suitability for use in explosive atmospheres.
It's crucial to note that ATEX rated chain blocks must be used in accordance with the manufacturer's instructions and within the specified hazardous area classifications. They should be inspected, maintained, and operated by trained personnel who understand the specific safety requirements and precautions associated with explosive environments.
If you require ATEX rated chain blocks for a particular application, consult with reputable suppliers or manufacturers who specialize in providing equipment for hazardous environments. They can provide detailed information on the specific ATEX ratings, certifications, and suitability of chain blocks for your intended use.
What are some good brands of Chain Block?
There are several reputable brands that manufacture high-quality chain blocks. While individual preferences may vary based on specific needs and regional availability, here are some well-known brands that are recognized for their reliable chain blocks:
William Hackett
Tiger
Elephant
Yale: Yale is a renowned brand that offers a wide range of lifting and material handling equipment, including chain blocks. They are known for their durability, safety features, and precise engineering.
KITO: KITO is a global leader in the production of high-quality lifting equipment, including chain blocks. Their chain blocks are known for their robust construction, smooth operation, and compliance with international standards.
Columbus McKinnon: Columbus McKinnon is a trusted manufacturer of lifting and motion control products, including chain blocks. Their chain blocks are designed for reliable performance, ease of use, and are available in various capacities.
Demag: Demag, a part of the Terex Corporation, is known for its comprehensive range of lifting solutions, including chain blocks. They offer a wide selection of chain blocks with different capacities and configurations to meet various lifting requirements.
Harrington Hoists: Harrington Hoists is a respected manufacturer of lifting equipment, including chain blocks. Their chain blocks are known for their durability, precision, and adherence to safety standards.
Ingersoll Rand: Ingersoll Rand is a trusted brand that produces a range of industrial equipment, including chain blocks. Their chain blocks are designed for rugged applications and are known for their reliability and performance.
Is it better to hire or buy Chain Blocks?
Whether to hire or buy chain blocks depends on your specific needs, frequency of use, budget, and other factors. Here are some considerations to help you make an informed decision:
Hiring Chain Blocks
- Cost: Hiring chain blocks can be cost-effective if you have occasional or short-term lifting needs. Instead of investing a significant amount upfront, you pay a rental fee for the duration of use.
- Flexibility: Hiring chain blocks provides flexibility as you can rent different capacities or configurations based on the specific lifting requirements of each project. This allows you to adapt to different tasks without the need for long-term commitment or storage.
- Maintenance: With hired chain blocks, the responsibility for maintenance and servicing usually rests with the rental company. They are responsible for ensuring that the equipment is in proper working condition, reducing your maintenance efforts and costs.
- Expertise: Rental companies often have knowledgeable staff who can guide you in selecting the appropriate chain block for your specific needs and provide support during operation.
Buying Chain Blocks
- Long-term Use: If you have frequent or ongoing lifting needs, buying chain blocks can be a more cost-effective option in the long run. Owning the equipment allows you to avoid continuous rental fees.
- Customization: Buying chain blocks gives you the freedom to select the specific capacity, length, and features that best suit your requirements. You can choose a chain block that precisely matches your needs without relying on available rental options.
- Availability: When you own chain blocks, you have immediate access to them whenever you need them. There's no dependence on rental availability or the risk of rental equipment being unavailable during peak times.
- Familiarity: Owning chain blocks allows you to become familiar with the equipment, its operation, and maintenance requirements over time. This can enhance efficiency and productivity in the long run.
- Investment: While buying chain blocks requires an upfront investment, the equipment can hold value and potentially be resold if no longer needed. This can provide some return on your investment.
Are Chain Blocks heavy?
The weight of chain blocks can vary depending on their capacity and size. Generally, chain blocks are designed to be relatively compact and portable, but they can still have some weight due to their construction and load capacity.
The weight of a chain block primarily depends on their capacity and chain length.
Capacity: Chain blocks come in various capacities, ranging from lighter-duty models with lower weight capacities to heavier-duty models capable of lifting several tons. As the capacity increases, the size and weight of the chain block tend to increase accordingly.
Length of Load Chain: The length of the load chain can also affect the weight of the chain block. Longer load chains may add additional weight, but they allow for greater lifting heights or reach.
Do Chain Blocks have brakes?
Yes, chain blocks typically have braking mechanisms to enhance safety and control during lifting operations. The brakes in chain blocks serve to secure and hold the load at a desired position, preventing unintended load movement or slippage. They help maintain the load's position when the operator releases tension on the hand chain or when the chain block is not actively lifting or lowering a load. Brakes are an essential component of chain blocks and contribute to their safe and efficient operation.
The braking system in a chain block typically consists of a load brake or a Weston-style brake. The load brake is engaged by the load chain passing through a braking mechanism, applying pressure to prevent the load from descending when tension is released from the hand chain. The load brake is designed to provide friction and hold the load securely in place.
It's important to note that the braking capacity of a chain block should match or exceed the intended load weight. Always adhere to the manufacturer's guidelines and recommendations for proper usage and ensure that the brake is functioning correctly during operation. Regular inspections and maintenance of the braking system are essential to ensure its effectiveness and safety.
How do you make Chain Blocks go up or down?
To make a chain block go up or down, you need to operate the hand chain attached to the chain block. The hand chain is a looped chain that you pull or release to control the movement of the load. Here's a step-by-step guide on how to use a chain block to lift or lower a load:
Attach the Chain Block: Securely attach the chain block to a suitable anchor point or lifting structure using a lifting hook, clevis, or other appropriate means. Ensure that the attachment point can support the weight of the load.
Position the Load: Position the load securely beneath the chain block, ensuring it is centered and balanced. Use appropriate lifting accessories such as slings or hooks to attach the load to the lifting hook of the chain block.
Engage the Brake: Before starting the lifting operation, ensure that the load brake is engaged. The brake should hold the load in position and prevent it from descending when no force is applied to the hand chain.
Lifting: Begin the lifting process by pulling the hand chain in a downward motion. Apply a steady and even force on the hand chain to raise the load. The chain block's gears and mechanisms will engage, allowing the load chain to pass through the block and lift the load.
Lowering: To lower the load, apply a controlled and gradual force on the hand chain in an upward motion. This action will release the load chain, allowing it to descend and lower the load. Ensure that you maintain a firm grip on the hand chain and control the descent speed to prevent sudden drops.
Operation and Safety: While operating the chain block, always follow the manufacturer's instructions and safety guidelines. Be aware of the load capacity limits, avoid overloading, and operate the chain block smoothly and steadily to maintain control over the load.
It's crucial to receive proper training and familiarize yourself with the specific chain block model you are using. Always prioritize safety, use appropriate personal protective equipment, and follow industry best practices and regulations when operating chain blocks or performing lifting operations.
How do you inspect Chain Blocks to make sure they're safe to use?
Inspecting chain blocks before use is essential to ensure their safety and proper functioning. Here are some steps to follow when inspecting a chain block:
Visual Inspection: Start by visually inspecting the chain block for any obvious signs of damage, wear, or deformation. Look for cracks, bends, corrosion, or missing components. Check the load chain, hooks, and other parts for signs of excessive wear, distortion, or elongation. Pay attention to the condition of the load-bearing components.
Load Chain Inspection: Examine the load chain links for any signs of stretching, wear, or damage. Look for elongation, twisting, or bending of individual links. Ensure that the load chain is properly lubricated and moves freely without any significant resistance or binding.
Hooks Inspection: Inspect the hooks for any signs of wear, cracks, or deformations. Ensure that the hook latch operates correctly, springs back into position, and securely holds the load. Verify that the hook is not twisted or bent and that the throat opening is within acceptable limits.
Brake System Inspection: Check the brake mechanism of the chain block. Ensure that the load brake engages and disengages smoothly and holds the load securely when the hand chain is released. Verify that the brake components are in good condition and free from excessive wear or damage.
Label and Markings: Ensure that the chain block has clear and legible labels, markings, and identification tags. These should include the manufacturer's name, capacity rating, serial number, and relevant certifications or standards compliance.
Operational Check: Perform an operational check by lifting a light load or applying a slight tension to the chain block. Observe the operation of the hand chain, load chain, and brake system. Ensure that the chain block moves smoothly and that the load is securely held when the hand chain is released.
Documentation and Maintenance: Keep records of inspections, maintenance, and any repairs or replacements performed on the chain block. Follow the manufacturer's recommended maintenance schedule and procedures for lubrication, cleaning, and servicing.
If any defects, damage, or abnormalities are identified during the inspection, the chain block should be taken out of service immediately and repaired or replaced as necessary. It is important to consult with the manufacturer's instructions and guidelines or seek professional assistance if needed.
Regular inspections should be conducted before each use, and more detailed inspections may be required periodically based on usage frequency, environmental conditions, and regulatory requirements.
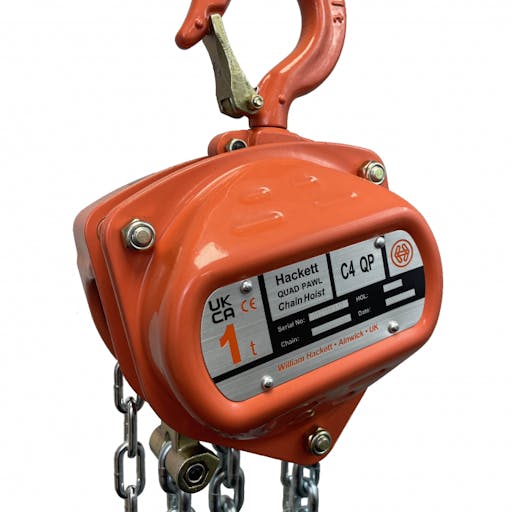