26.05.23
Everything you need to know about Excavators
What are Excavators?
Excavators are heavy construction equipment commonly used in various industries, including construction, mining, and landscaping. They are designed to dig, move, and lift large quantities of materials, such as soil, rocks, and debris. Excavators are known for their versatility and can be equipped with a wide range of attachments to perform different tasks.
Typically, an excavator consists of a cab mounted on a rotating platform called the "house" or "upper," an articulated arm known as the "boom," and an attachment called the "bucket" at the end of the boom. The boom is connected to the house with a hinge, allowing it to swing horizontally. The bucket can be changed to accommodate various tasks, such as digging, lifting, and demolition.
Excavators are powered by hydraulic systems that enable precise control and efficient operation. They use hydraulic cylinders and motors to move the boom, bucket, and other attachments. The operator sits in the cab and controls the excavator's movements using joysticks, pedals, and switches.
Excavators come in various sizes, ranging from compact models weighing a few thousand pounds to large machines weighing several tons. The size and specifications of an excavator depend on the intended use and the scale of the projects it will be involved in.
What are the best Mini Excavator brands
There are several reputable brands that manufacture mini excavators known for their quality, performance, and reliability. The "best" brand can depend on factors such as specific needs, preferences, availability, and regional considerations. Here are some well-regarded mini excavator brands:
1. Kubota: Kubota is a well-known manufacturer of compact construction equipment, including mini excavators. They offer a range of models with various sizes and features, known for their durability, fuel efficiency, and operator comfort.
2. Bobcat: Bobcat is a renowned brand in the compact equipment industry. Their mini excavators are recognized for their versatility, maneuverability, and strong digging capabilities. Bobcat's machines often come with advanced features and technology for enhanced performance.
3. Caterpillar: Caterpillar, or CAT, is a globally recognized brand that produces a wide range of construction equipment, including mini excavators. CAT mini excavators are known for their power, reliability, and innovative features that enhance productivity and operator comfort.
4. Takeuchi: Takeuchi specializes in manufacturing compact construction machinery, including mini excavators. Their machines are known for their strong digging forces, excellent stability, and efficient hydraulic systems. Takeuchi mini excavators are popular for their durability and overall performance.
5. Yanmar: Yanmar offers a range of mini excavators that are highly regarded for their reliability, fuel efficiency, and compact design. Their machines are known for their smooth operation, advanced technology, and ease of maintenance.
6. JCB: JCB is a reputable manufacturer of construction equipment, including mini excavators. Their mini excavators are recognized for their durability, innovative features, and operator-friendly design. JCB's machines often come with advanced safety features and efficient hydraulic systems.
These are just a few notable brands in the mini excavator market. It's important to research and consider factors such as specific model features, local dealer support, parts availability, and overall reputation when choosing the best mini excavator brand for your specific needs.
Excavator Components
Excavators are complex machines with various components working together to perform their tasks efficiently. Here are the main components of an excavator:
1. Boom: The boom is a large, hinged arm that supports the digging attachment and allows vertical and horizontal movement. It provides reach and lifting capacity to the excavator.
2. Arm (Dipper): The arm, also known as the dipper, is attached to the end of the boom. It connects the boom to the bucket or other attachments and controls the digging depth and angle.
3. Bucket: The bucket is the attachment at the end of the arm and is used for digging, scooping, and loading materials. Buckets come in various sizes and types, including general-purpose buckets, digging buckets, grading buckets, and specialized buckets for specific applications.
4. Hydraulic Cylinders (Rams): Hydraulic cylinders, also called rams, are responsible for providing the power and force to control the movement of the boom, arm, bucket, and other attachments. They consist of a piston, rod, cylinder, and hydraulic seals.
5. Tracks or Tires: Excavators can have either tracks or tires for mobility, depending on the model and purpose. Tracks provide stability, traction, and maneuverability on various terrains, while tires offer faster travel speeds and better mobility on paved surfaces.
6. Operator's Cabin: The operator's cabin is the enclosed space where the operator sits and controls the excavator. It typically features ergonomic controls, a seat, instrument panel, and windows for visibility.
7. Engine: The engine provides the power to operate the excavator's hydraulic system, tracks (if equipped), and other auxiliary functions. Excavators generally use diesel engines for their power and torque.
8. Hydraulic System: The hydraulic system is crucial for the operation of excavators. It controls the movement of the boom, arm, bucket, and other attachments using hydraulic fluid, hydraulic pumps, valves, and hoses. The hydraulic system provides the force and precision required for excavating and lifting operations.
9. Undercarriage: The undercarriage consists of the tracks (or tires), track or wheel frames, rollers, idlers, and sprockets. It supports the weight of the excavator and allows for smooth movement and stability.
10. Counterweight: The counterweight is located at the rear of the excavator and provides balance and stability. It helps offset the weight of the front attachments and prevents the excavator from tipping forward during operation.
11. Control System: Excavators feature control systems that allow the operator to manipulate the machine's movements and functions. These systems include joysticks, foot pedals, buttons, or levers that control the hydraulic functions, boom/arm/bucket movement, and other operations.
These are the primary components of an excavator, although there may be additional features and accessories depending on the specific model and purpose of the machine.
Do you need a license to operate an Excavator in the UK?
In the UK, you generally don't need a specific license to operate an excavator on private land. However, there are regulations and requirements in place to ensure safe operation. Here are some key points to consider:
1. Construction Plant Competence Scheme (CPCS): The Construction Plant Competence Scheme is a widely recognized certification scheme in the UK. It provides proof of competence for operating various types of construction plant machinery, including excavators. The CPCS certification is not a legal requirement, but it is often preferred by employers and construction companies as evidence of competency.
2. Health and Safety Regulations: Employers have a legal responsibility to ensure that operators are trained and competent to operate excavators safely. The Health and Safety at Work Act 1974 and other associated regulations, such as the Provision and Use of Work Equipment Regulations (PUWER) and the Lifting Operations and Lifting Equipment Regulations (LOLER), outline the requirements for safe plant operation.
3. Training and Competency: It is highly recommended to undergo appropriate training and gain practical experience before operating an excavator. Training courses provided by accredited training providers can offer valuable knowledge and skills necessary for safe and efficient operation. Training courses may include both theory and practical elements, covering topics such as machine controls, safety procedures, and operating techniques.
4. Construction Industry Scheme (CIS): For individuals working in the construction industry, being registered under the Construction Industry Scheme is required. Registration involves obtaining a Unique Taxpayer Reference (UTR) number and following specific tax obligations. This registration is applicable if you are self-employed or working as a subcontractor in the construction sector.
While there is no specific license requirement for operating excavators on private land in the UK, it is essential to have the necessary training, competence, and understanding of health and safety regulations. Employers and construction sites may have their own requirements and may prefer operators who hold CPCS certification or equivalent qualifications. It is always advisable to check with potential employers or relevant regulatory bodies for specific requirements in your area or industry.
Zero tail swing Excavators
Zero tail swing excavators, also known as zero-radius excavators or zero-swing excavators, are a specific type of excavator design that allows for minimal or zero tail overhang when the machine rotates. In other words, the counterweight of a zero tail swing excavator does not extend beyond the width of the tracks or undercarriage.
The key feature of zero tail swing excavators is their ability to rotate within the footprint of the machine. This makes them particularly useful in confined or tight spaces, such as urban areas or construction sites with limited maneuvering room. The lack of tail overhang minimizes the risk of the excavator accidentally striking nearby obstacles or structures when rotating.
The benefits of zero tail swing excavators include:
- Improved Manoeuvrability: With their compact design and zero tail overhang, these excavators can easily operate and navigate in narrow spaces, close to walls, or near other obstacles.
- Enhanced Safety: The reduced risk of the excavator's rear end swinging into objects or people improves overall safety on the worksite, especially in congested areas.
- Efficient Space Utilization: Zero tail swing excavators maximize the utilization of available workspace, allowing operators to work more effectively in restricted areas without compromising performance.
- Versatile Applications: These excavators are suitable for various tasks, including excavation, digging, lifting, demolition, and utility work, especially in urban environments or job sites with limited access.
Zero tail swing excavators come in different sizes and configurations to suit specific project requirements. It's important to note that while the rear of the machine is designed to minimize overhang, the front-end movement and reach are not impacted, ensuring full functionality and performance.
Kubota Excavator models
Kubota offers a range of excavator models designed for various applications. Here are some popular Kubota excavator models along with their approximate weights in kilograms (kg):
- Kubota K008-5: Operating Weight: 975kg
- Kubota U10-5: Operating Weight: 1,125 kg
- Kubota KX015-4: Operating Weight: 1,420kg
- Kubota U17-3: Operating Weight: 1,755 kg
- Kubota KX018-4: Operating Weight: 1,725 kg
- Kubota KX71-3: Operating Weight: 2,600 kg
- Kubota U27-4: Operating Weight: 2,675 kg
- Kubota KX057-4: Operating Weight: 5,380 kg
- Kubota U55-4: Operating Weight: 5,500 kg
- Kubota KX080-4: Operating Weight: 8,270 kg
Differences between the Kubota k008 and u10 models
The Kubota K008 and Kubota U10 are both compact excavator models offered by Kubota, but they have some key differences in terms of size, weight, and capabilities. Here are the main differences between the Kubota K008 and Kubota U10:
Size and Weight:
- The Kubota K008 is the smaller and lighter of the two models. It is classified as a micro-excavator and is designed for extremely tight spaces and restricted access areas. It has a compact size and lower weight, making it easier to maneuver and transport.
- The Kubota U10, on the other hand, is slightly larger and heavier than the K008. It is classified as a mini-excavator and provides a bit more power and capacity compared to the K008
- The Kubota K008 typically has a digging depth of around 1.65 meters (5.4 feet) and a reach of approximately 3 meters (9.8 feet). It is suitable for small-scale digging and trenching tasks
- The Kubota U10 offers a greater digging depth and reach. It usually has a digging depth of around 1.8 meters (5.9 feet) and a reach of approximately 3.2 meters (10.5 feet). This increased capability allows for more versatile digging and excavation operations.
Engine Power:
- The Kubota K008 is equipped with a smaller engine compared to the Kubota U10. The exact specifications may vary depending on the model year and configuration, but generally, the K008 has a lower horsepower rating.
- The Kubota U10 features a more powerful engine, providing higher horsepower and torque, enabling it to handle heavier workloads and tougher conditions.
- The control systems on the Kubota K008 and Kubota U10 may differ slightly. It's important to familiarize yourself with the specific control layout and functionality of each model.
These are some of the key differences between the Kubota K008 and Kubota U10 compact excavator models. Depending on the specific requirements of your project and the available space, one model may be more suitable than the other. It's recommended to consult with a Kubota dealer or representative to determine the best fit for your needs.
What is a Deadman on an Excavator and what does it do?
In the context of an excavator, a "deadman" refers to a safety device or feature that is typically present in the operator's compartment. The deadman function is designed to enhance operator safety by ensuring that certain controls or functions are engaged only when the operator is actively present and applying pressure.
The specific implementation of the deadman feature may vary depending on the excavator model and manufacturer, but its primary purpose is to prevent unintended movement or operation of the excavator when the operator is not in control or in case of an emergency. Here are a few common aspects of the deadman feature on an excavator:
1. Operator Presence Control: The deadman feature often involves an operator presence control system. This can be in the form of a pressure-sensitive switch, pedal, or lever that the operator needs to engage or maintain pressure on to enable the operation of certain functions.
2. Automatic Function Deactivation: If the operator releases pressure or disengages the operator presence control, the excavator's deadman feature will automatically deactivate or disengage certain functions. This helps prevent unintended operation or movement of the machine.
3. Emergency Stop Function: In some cases, the deadman feature may incorporate an emergency stop function. This allows the operator to quickly stop all machine functions by activating a dedicated emergency stop button or switch. It provides a rapid response to halt the machine in critical situations.
Lifting points on Excavators
Excavators typically have lifting points or lifting provisions to enable them to be lifted or transported by other equipment, such as cranes or transport trucks. These lifting points are specifically designed and reinforced areas on the excavator structure that can safely support the weight of the machine during lifting.
The specific location and design of lifting points can vary depending on the excavator model and manufacturer. However, some common lifting points on excavators include:
1. Lifting Eyes or Hooks: These are usually located on the upper structure or superstructure of the excavator, such as on the counterweight or the frame. They are often large, sturdy metal loops or hooks that can be connected to lifting equipment.
2. Lifting Lugs: These are solid metal plates or bars attached to the excavator's frame or superstructure, designed to provide secure attachment points for lifting. Lifting lugs are typically positioned symmetrically to ensure balanced lifting.
3. Lifting Rings or Clevises: These are circular or U-shaped attachments that are integrated into the excavator structure for lifting purposes. They are usually located on the upper structure or superstructure and provide secure connection points for lifting equipment.
It is important to note that when lifting an excavator, proper lifting techniques and safety precautions should be followed. This includes ensuring the lifting equipment is suitable for the weight and size of the excavator, using appropriate lifting slings or chains, and adhering to the excavator manufacturer's guidelines and recommendations for lifting and transport.
Transporting Excavators
When strapping an excavator onto a vehicle for transportation, it is crucial to prioritize safety to prevent accidents, damage, or injuries. Here are some steps to follow for safely strapping an excavator onto a vehicle:
1. Select Appropriate Straps and Equipment: Use high-quality, heavy-duty straps specifically designed for securing heavy loads. Ensure that the straps have sufficient strength and load capacity to secure the weight of the excavator.
2. Position the Excavator: Place the excavator on the vehicle in the appropriate position, considering the weight distribution, center of gravity, and any vehicle-specific guidelines. Follow the manufacturer's recommendations for loading and securing the excavator.
3. Use Multiple Straps: Use multiple straps to secure the excavator from various angles and directions. Distribute the load evenly across the straps to ensure balanced tension and stability.
4. Attach Straps to Secure Points: Identify and attach the straps to strong and secure points on the excavator and the vehicle. Common secure points include designated tie-down points, structural components, or sturdy parts of the excavator, such as the boom or frame. Avoid attaching straps to fragile or vulnerable components.
5. Protect Contact Points: Place protective padding or cloth between the straps and the excavator's surfaces to prevent friction and potential damage during transportation. This is particularly important when securing straps around delicate or painted surfaces.
6. Tension the Straps: Apply tension to the straps gradually and evenly to secure the excavator. Use a tensioning device, such as a ratchet strap or winch, to tighten the straps securely. Ensure that the straps are tight enough to hold the excavator in place, but avoid over-tightening, which can cause damage.
7. Check and Recheck: Once the straps are in place, thoroughly inspect the entire setup to ensure that all connections are secure, and the excavator is stable. Double-check the tension of the straps to make sure they are tight and properly secured.
8. Test Stability: Before hitting the road, carefully test the stability of the excavator by applying gentle force from different directions. Check for any shifting or movement. If there is any instability, re-adjust the straps and re-tighten as necessary.
9. Regularly Monitor During Transport: During transportation, periodically check the straps to ensure they remain tight and secure. Make necessary adjustments if any slack or loosening is observed.
The size of the excavator that can fit on a trailer depends on several factors, including the size and weight capacity of the trailer, as well as the dimensions and weight of the excavator itself. Here are some general guidelines:
1. Trailer Size and Weight Capacity: Determine the size and weight capacity of the trailer you plan to use. Trailers come in various sizes and weight ratings, such as tandem axle trailers, low-bed trailers, or flatbed trailers. Check the manufacturer's specifications or consult with a trailer dealer to determine the trailer's maximum load capacity.
2. Excavator Dimensions: Consider the dimensions of the excavator, including its length, width, height, and weight. Measure the excavator accurately, taking into account any attachments or accessories that may affect its dimensions.
3. Legal Requirements: Ensure compliance with local laws and regulations regarding trailer and load dimensions, weight restrictions, and any permit requirements for transporting oversized or overweight loads.
Use of Dozer Blades on Excavators
Excavator dozer blades, also known as grading blades or bulldozer blades, are attachments specifically designed for excavators to perform tasks similar to those of a bulldozer. These blades are typically attached to the front of the excavator's boom or arm and can be raised, lowered, tilted, and angled to perform various grading, leveling, and earthmoving operations.
Here are some common uses of excavator dozer blades:
1. Grading and Leveling: The dozer blade attachment allows the excavator to push and level materials like soil, gravel, or sand. It is used to create even surfaces, slopes, or embankments on construction sites, road projects, or landscaping tasks.
2. Backfilling Trenches: When excavating trenches for utilities or drainage systems, the dozer blade can be used to push and distribute the excavated soil back into the trench, ensuring proper compaction and backfilling.
3. Spreading and Distribution: Excavator dozer blades are useful for spreading and distributing loose materials, such as gravel or aggregate, across a designated area. The blade can be adjusted to control the depth and thickness of the material being spread.
4. Snow Removal: In regions with snowy or icy conditions, excavator dozer blades can be used for snow removal operations. The blade can push, pile, or clear snow from roads, parking lots, or other areas.
5. Rough Grading and Site Preparation: Before more detailed grading work, the dozer blade can be employed for rough grading and initial site preparation, clearing debris, or pushing aside small obstructions.
6. Landscaping and Earthmoving: The versatility of the dozer blade attachment makes it useful for various landscaping tasks, including shaping and contouring land, moving soil or aggregates, and preparing the ground for landscaping features or structures.
What are the key differences between manual pin hitches and hydraulic quick hitches on Excavators, and which is better?
Manual pin hitches and hydraulic quick hitches are two different types of attachments used for connecting buckets and other tools to excavators. Here are the key differences between these two types:
Operation:
- Manual Pin Hitch: A manual pin hitch requires the operator to physically insert and remove pins to attach or detach the bucket. This process involves manually aligning the attachment with the coupler and securing it in place using pins or locks.
- Hydraulic Quick Hitch: A hydraulic quick hitch utilizes hydraulic cylinders and a locking mechanism to quickly and easily attach and detach buckets. It is operated by the excavator's hydraulic system, allowing the operator to engage or disengage the attachment from the comfort of the operator's compartment.
Speed and Efficiency:
- Manual Pin Hitch: Connecting and disconnecting attachments with a manual pin hitch is generally a slower process. It requires the operator to manually align the attachment, insert the pins, and secure them in place. This can be time-consuming, especially when frequently switching between multiple attachments.
- Hydraulic Quick Hitch: Hydraulic quick hitches offer a significant advantage in terms of speed and efficiency. With the press of a button or lever, the operator can engage or disengage the attachment quickly and effortlessly, without leaving the operator's compartment. This allows for rapid changes between different attachments, enhancing productivity and efficiency.
Operator Convenience and Safety:
- Manual Pin Hitch: While manual pin hitches are generally reliable, their operation requires the operator to physically interact with the attachment and coupler, potentially exposing them to hazards such as pinch points or heavy lifting.
- Hydraulic Quick Hitch: Hydraulic quick hitches enhance operator convenience and safety. The operator can remain inside the excavator, eliminating the need for manual handling of heavy pins or direct contact with the attachment. This reduces the risk of accidents, injuries, or strain on the operator.
Versatility and Compatibility:
- Manual Pin Hitch: Manual pin hitches are typically compatible with a wide range of attachments, as long as the pins and dimensions match. They are commonly used for smaller excavators and attachments with lower weight.
- Hydraulic Quick Hitch: Hydraulic quick hitches are available in various models to accommodate different excavator sizes and attachment types. They offer greater versatility, allowing operators to use a wider range of attachments quickly and efficiently.
In terms of which type is better, it depends on the specific needs and preferences of the operator and the nature of the tasks performed. Hydraulic quick hitches are generally favored for their speed, efficiency, convenience, and enhanced safety. However, manual pin hitches may still be suitable for certain applications where the frequency of attachment changes is low, or in situations where cost is a significant factor.
Excavator Maintenance
To keep excavators in good working order and ensure their longevity, regular maintenance and inspections are essential. Here are some maintenance and inspection tips for excavators:
- Follow the Manufacturer's Guidelines: Familiarize yourself with the manufacturer's recommended maintenance schedule and guidelines specific to your excavator model. Adhere to the prescribed intervals for routine maintenance tasks and inspections.
- Conduct Daily Pre-Start Checks: Before operating the excavator, perform a thorough pre-start inspection. Check the fluid levels, such as engine oil, hydraulic fluid, and coolant. Inspect the tires or tracks, lights, controls, safety features, and any attachments you'll be using. Look for leaks, loose components, or any signs of damage or wear.
- Lubrication: Keep the excavator properly lubricated according to the manufacturer's recommendations. Pay attention to greasing pivot points, joints, and other moving parts. This helps reduce friction, prevent premature wear, and maintain smooth operation.
- Filter Maintenance: Regularly inspect and replace the engine air filters, hydraulic filters, and fuel filters as recommended by the manufacturer. Clean or replace filters when they become dirty or clogged to ensure proper engine performance and prevent contaminants from damaging the system.
- Fluid Inspections: Check hydraulic fluid levels and inspect for any signs of contamination, such as water or debris. Inspect engine oil regularly and change it at the recommended intervals. Monitor coolant levels and ensure the coolant mixture is appropriate for the operating conditions.
- Track Maintenance: If your excavator has tracks, regularly inspect them for signs of wear, damage, or loose components. Ensure the tracks are properly tensioned. If your excavator has tires, check the tire pressure and look for signs of wear or damage. Rotate the tires if necessary to promote even wear.
- Electrical System: Inspect the electrical system, including the battery, wiring, and connectors. Clean any corrosion from the battery terminals and ensure a secure connection. Check the lights, gauges, and controls to ensure they are functioning correctly.
- Inspect Hydraulic Hoses and Fittings: Regularly inspect hydraulic hoses and fittings for leaks, cracks, or signs of wear. Replace damaged hoses or fittings promptly to prevent hydraulic system failures.
- Cleanliness: Keep the excavator clean from dirt, debris, and mud. Use compressed air or water to clean hard-to-reach areas. Remove debris from radiator fins and other cooling components to maintain proper cooling.
- Operator Training: Ensure that operators are properly trained in the operation and maintenance of the excavator. Encourage them to report any abnormalities or concerns promptly.
Remember, it is important to consult the excavator's specific manual and guidelines provided by the manufacturer for comprehensive maintenance instructions and safety precautions. Regular maintenance and inspections help identify potential issues early, prevent breakdowns, and extend the lifespan of your excavator.
While mini excavators are generally reliable machines, there are a few common issues that can occur. Taking preventive measures and following proper maintenance practices can help minimize these issues. Here are some common problems with mini excavators and tips to prevent them:
1. Hydraulic System Leaks: Hydraulic fluid leaks can occur in hoses, fittings, or seals within the hydraulic system. Regularly inspect hydraulic lines, hoses, and fittings for signs of leakage, such as puddles of fluid or oil stains. Promptly repair or replace damaged components and ensure proper tightening of connections.
2. Track/Tire Wear or Damage: Mini excavators equipped with tracks can experience track wear, track tension issues, or track damage. Similarly, those with tires may face tire wear or punctures. Inspect tracks or tires regularly for signs of wear, such as worn treads or sidewall damage. Adjust track tension as per manufacturer guidelines, and replace worn tracks or tires promptly.
3. Electrical System Malfunctions: Electrical issues can occur in the wiring, connectors, or components of the mini excavator's electrical system. Keep electrical connections clean and free from corrosion. Regularly inspect wiring harnesses for damage or loose connections. Address any electrical malfunctions promptly to prevent further damage.
4. Engine Overheating: Overheating can be caused by clogged or dirty cooling system components, insufficient coolant levels, or a malfunctioning radiator or fan. Clean the radiator and cooling system regularly to prevent debris buildup. Monitor coolant levels and ensure proper coolant mixture. Regularly inspect the radiator and fan for damage or malfunctions.
5. Component Wear: Various components of mini excavators, such as pins, bushings, and undercarriage parts, can experience wear over time. Implement a regular inspection routine to identify worn components. Lubricate pivot points and moving parts as recommended by the manufacturer. Replace worn parts promptly to prevent further damage or breakdowns.
6. Fuel System Issues: Fuel-related problems can arise from contaminated fuel, clogged filters, or issues with injectors. Use clean fuel from reputable sources and regularly replace fuel filters according to the manufacturer's recommendations. Monitor fuel system performance and address any issues promptly.
7. Operator Error or Improper Usage: Operator error or improper usage can lead to unnecessary strain on the machine, increased wear, and potential breakdowns. Provide proper operator training on the correct operation and handling of the mini excavator. Emphasize safe operating practices, such as avoiding excessive loads, not exceeding weight limits, and following recommended operating procedures.
Regular maintenance, adherence to manufacturer guidelines, and timely repairs are key to preventing common issues with mini excavators. Consult the operator's manual for specific maintenance requirements, conduct routine inspections, and address any identified issues promptly to keep your mini excavator in optimal working condition.
Maintenance of hydraulic rams on Excavators
Rams, also known as hydraulic cylinders, are an essential component of excavators. They are responsible for generating the force required to operate various hydraulic functions, such as the movement of the boom, arm, bucket, or other attachments. Rams consist of a piston, rod, cylinder, and hydraulic seals.
To prevent damage to the rams on excavators, here are some preventive measures:
1. Regular Inspections: Perform routine inspections of the rams to check for signs of damage, leakage, or wear. Look for oil leaks, abnormal movement, or scoring on the rod or cylinder. Inspect hydraulic seals for signs of wear or degradation. If any issues are detected, address them promptly to prevent further damage.
2. Keep Rams Clean: Maintain a clean working environment to prevent debris, dirt, or other contaminants from entering the hydraulic system. Clean the rams and surrounding areas regularly, especially after working in dusty or muddy conditions. This helps prevent abrasive particles from causing damage to the cylinder or seals.
3. Proper Lubrication: Ensure that the rams are properly lubricated according to the manufacturer's recommendations. Lubrication helps reduce friction and wear on the seals and moving parts of the rams. Use the recommended lubricants and follow the specified intervals for lubrication.
4. Avoid Overloading: Avoid exceeding the load or weight capacity of the excavator. Overloading the machine can put excessive stress on the rams, leading to potential damage or failure. Follow the manufacturer's guidelines for operating limits and load capacities to prevent unnecessary strain on the rams.
5. Maintain Correct Hydraulic Pressure: Ensure that the hydraulic system is operating within the specified pressure range. Excessive pressure can lead to increased stress on the rams, while insufficient pressure may result in ineffective operation. Regularly check and maintain the hydraulic pressure within the recommended range.
6. Operator Training: Provide proper training to operators on the correct operation of the excavator, including the use of hydraulic functions. Emphasize safe operating practices and educate operators on the limitations and capabilities of the machine. Improper or careless operation can put excessive strain on the rams and other components.
7. Prompt Repairs: If any issues or damage are detected in the rams, such as leaks or excessive wear, address them promptly. Repair or replace damaged or worn components as soon as possible to prevent further damage and ensure the proper functioning of the rams.
By following these preventive measures, you can help extend the lifespan of the rams on excavators and maintain their optimal performance. Regular inspections, cleanliness, proper lubrication, and safe operating practices are crucial for preventing damage to the rams and ensuring the efficient operation of the excavator.
Maintaining Excavator Tracks
Proper maintenance of tracks on mini excavators is crucial to prevent tearing or coming off. Here are some maintenance tips to help keep the tracks in good condition:
1. Regular Inspection: Conduct regular visual inspections of the tracks to check for signs of wear, damage, or loose components. Look for any tears, cuts, missing track pads, or damaged links. If any issues are detected, address them promptly to prevent further damage.
2. Clean Tracks: Keep the tracks clean by removing dirt, mud, rocks, or other debris that may accumulate. Debris can get lodged between the track links, causing premature wear or track misalignment. Use a high-pressure water hose or a brush to clean the tracks thoroughly.
3. Maintain Proper Track Tension: Maintaining the correct track tension is important for track longevity and performance. Tracks that are too loose can increase the risk of derailing, while tracks that are too tight can cause excessive wear. Follow the manufacturer's guidelines to adjust the track tension properly.
4. Lubricate Track Components: Regularly lubricate the track components, such as the track links, pins, and bushings, to minimize friction and wear. Use the recommended lubricant and follow the manufacturer's instructions for lubrication intervals.
5. Check and Replace Track Components: Keep an eye on the condition of individual track components, including track pads, track links, pins, and bushings. Replace any worn or damaged components promptly to ensure proper track performance and prevent further damage.
6. Avoid Excessive Sideways Forces: Minimize the application of excessive sideways forces on the tracks. Sharp turns or operating on uneven terrain can put undue stress on the tracks and increase the risk of tearing or coming off. Practice smooth, controlled movements to reduce strain on the tracks.
7. Avoid Overloading: Avoid overloading the mini excavator, as excessive weight can strain the tracks and lead to damage. Operate within the specified load capacity and avoid carrying loads beyond the machine's capabilities.
8. Follow Safe Operating Practices: Train operators to follow safe operating practices, such as avoiding sudden, jerky movements and minimizing impacts on the tracks. Encourage operators to be mindful of the terrain and make adjustments accordingly to prevent excessive strain on the tracks.
9. Regular Maintenance Schedule: Implement a regular maintenance schedule for the mini excavator, including track inspections, cleaning, and lubrication. Adhere to the manufacturer's recommended maintenance intervals and procedures.
By following these maintenance practices, you can help extend the lifespan of the tracks on mini excavators and reduce the risk of tearing or coming off. Regular inspections, cleaning, proper tension, and timely component replacement are key to maintaining the tracks in good working order.
Please note that the weights provided are approximate and can vary based on the specific configuration, attachments, and optional extras added to the excavators. It's always recommended to refer to the manufacturer's specifications or consult with a Kubota dealer for the most accurate and up-to-date information on their excavator models and their respective weights.
Greasing & Lubrication of Excavators
Grease points on excavators are specific locations where lubricating grease needs to be applied to ensure proper lubrication of moving parts. Greasing these points helps reduce friction, prevent wear, and extend the lifespan of critical components. Here's some information about grease points on excavators:
Location of Grease Points:
- Grease points can vary depending on the specific model and manufacturer of the excavator. They are typically found at pivot points, joints, and moving parts where metal components interact. Common grease points include bucket pins, swing bearing, boom and arm pivot points, linkage connections, and track components.
When to Apply Grease:
- Regular greasing should be part of your routine maintenance schedule for the excavator. The frequency of greasing depends on factors such as operating hours, working conditions, and the manufacturer's recommendations. It's generally recommended to grease the excavator at least once every 50-100 operating hours or as specified by the manufacturer.
Best Practices for Applying Grease:
1. Preparation: Before applying grease, clean the grease fittings and surrounding areas to remove dirt, debris, and old grease. This prevents contaminants from entering the components when new grease is applied.
2. Select the Right Grease: Use the type and grade of grease recommended by the excavator manufacturer. The correct grease will ensure optimal lubrication and compatibility with the machine's components.
3. Grease Gun and Attachment: Use a high-quality grease gun with a flexible hose attachment to access hard-to-reach grease points. The attachment should securely fit onto the grease fitting to prevent grease leakage.
4. Apply the Right Amount: Apply an appropriate amount of grease to each grease point. Over-greasing can lead to excess buildup and potential damage, while under-greasing may result in insufficient lubrication. Refer to the manufacturer's guidelines to determine the recommended amount of grease for each point.
5. Pump Grease Slowly and Steadily: Slowly and steadily pump the grease into the fitting while monitoring for resistance. Avoid pumping too quickly, as it can lead to excessive pressure and potential damage to seals or fittings.
6. Observe Lubricant Overflow: As you pump grease into the fitting, watch for grease to start coming out from adjacent areas. This indicates that the grease has filled the cavity and excess grease is being pushed out, ensuring proper lubrication.
7. Wipe Excess Grease: After greasing, wipe away any excess grease to maintain cleanliness and prevent accumulation of dirt and debris.
Remember to consult the excavator's manual or contact the manufacturer for specific information regarding grease points and recommended greasing procedures for your particular model. Following proper greasing practices will help ensure the longevity and optimal performance of your excavator's moving parts.
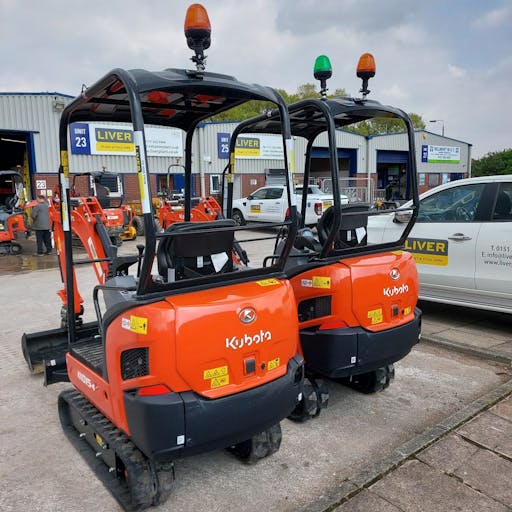